Similar Posts
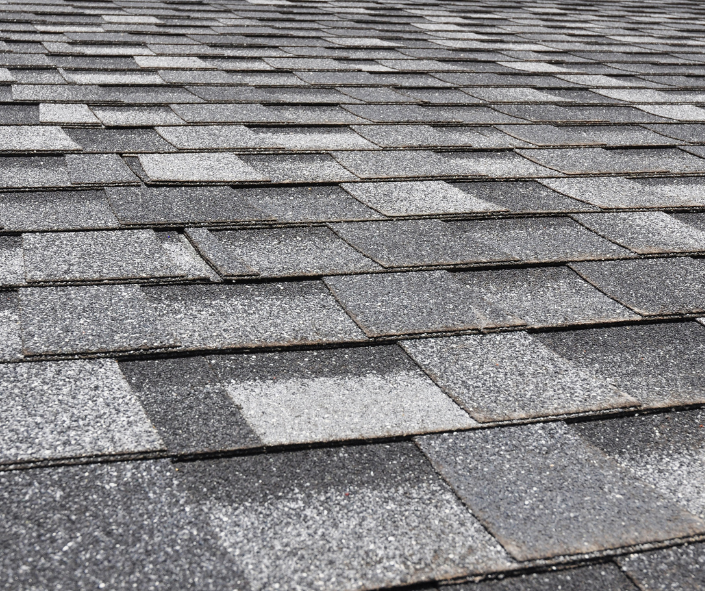
Doing it this way for 30 years.
We’ve all heard someone say, “I’ve been doing it this way for 30 years.” The first thing toconsider is whether that is a good thing or a bad thing? Answering that question really depends on…
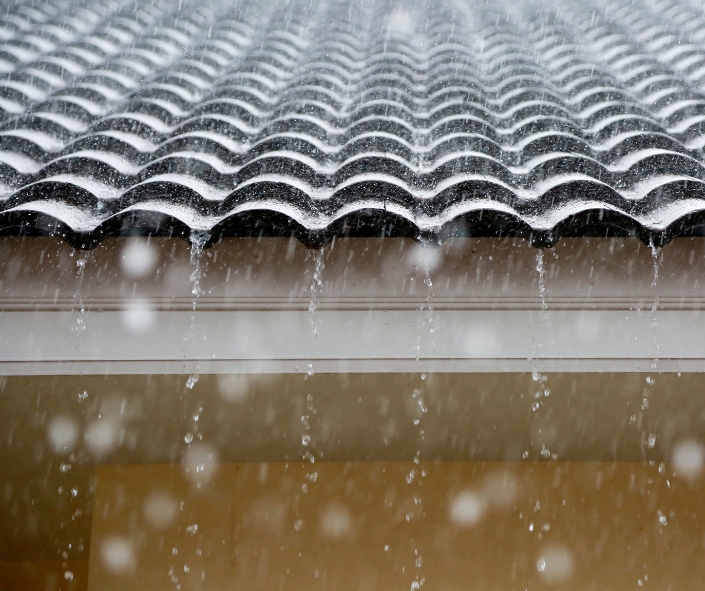
If it doesn’t get wet, it won’t leak.
At the end of January, we, at Polyguard, inaugurated a new training center with our first air barrier installation training event. The event was a fantastic success, and though I can’t take the credit, I…
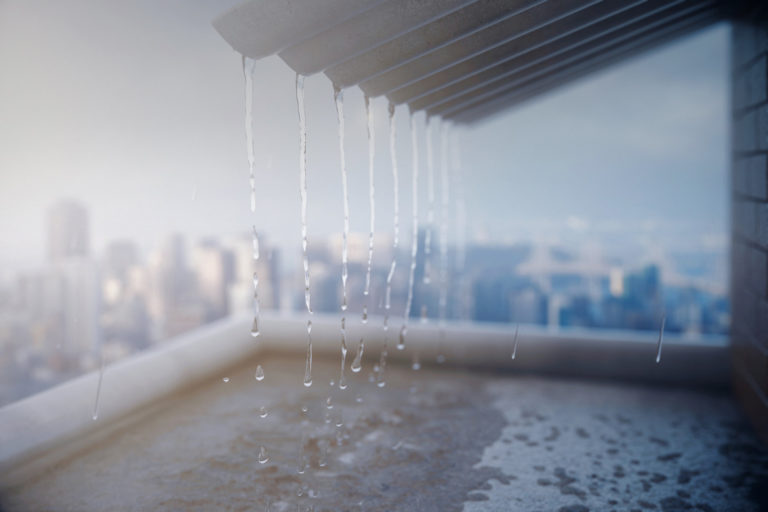
Keeping the Outside Out, and the Inside In.
Why do we construct Buildings? The answer is quite simple; we construct buildings to provide shelter for human activities. If that is the reason, then why does the vision appear to be lost? It is…